Trusted by:
Build the future of connectivity with our turnkey IoT application development services
With over 20 years of software engineering experience, Daffodil Software has been developing and customizing software and mobile apps for clients in multiple industries such as healthcare, oil & gas, and media & entertainment. As a leading IoT software development company, we aim at delivering robust, scalable, and feature-rich IoT solutions for our customers. With our systematic development & data-driven decision-making approach, we help you to transform your ideas into visions and provide real-time data connections with other IoT systems over the internet. We hold experience working with 100+ clients across the globe in various software development, mobile apps development, technology innovation, and other trending domains.
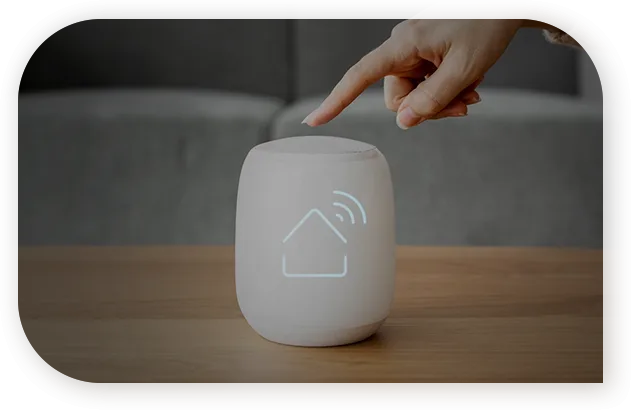
We help you:
Our IoT software development services include
IoT strategy and advisory
Get expert consultation around defining the problem statement along with recommendations on the solution blueprint. Develop a roadmap of your business with us, design custom IoT devices & sensors, and ensure effective & quick solution advisory for your IoT-based needs emphasizing the best industry practices.
IoT application development
End-to-end development of custom IoT applications for various industries and domains ranging from requirement understanding, user-story orchestration, engineering, architecture design, platform, and user app creation, testing, maintenance, and support.
Intralogistics solutions
Custom intralogistics and asset-tracking IoT solutions specific to your logistic needs, business needs, employee processes, and assets. Our robust and inter-connected IoT application development services can also help you reduce risk, improve ROI, and generate new revenue models to enable you to track your equipment or vehicles in real time.
Wearable technology
Develop embedded software for different wearable-optimized IoT devices and wearable tech trends being utilized in various industries such as healthcare, retail, hospitality, etc. Our expertise in development ensures the seamless integration of wearable devices with other IoT devices.
System integration
Our team of IoT experts helps you seamlessly integrate various IoT-enabled devices with business management software, ERP, CRM, SMS, email clients, etc. Make data-backed decisions with us with real-time data flow and intuitive data visualization techniques. We also create an IoT platform for you to enable monitoring, communicating, and managing IoT devices and data, along with seamless data exchange on cloud platforms.
IoT solution testing
Rigorous testing of IoT devices and software to test conformance with standards, interoperability, security, load management, etc. Ensure a flawless experience through IoT application development solutions creating robust and bug-free IoT applications.
Setup a free consulting session with our IoT software development experts
Client Success Stories
Our custom IoT software development services for end users & businesses
Industrial IoT
We use machine vision systems and wireless inventory trackers to track IoT devices and inventories, respectively as well as make rapid changes by detecting any defect or requirement. Our predictive maintenance can forecast a fault before its occurrence in your IoT systems and human-machine interface (HMI) permits the user to remotely interact with machines.
Consumer IoT
Bring your IoT-based peripherals and wearables like smart apparel & accessories to the advanced level with our IoT software development services. With our IoT-based tracking solutions, smart home systems, smart sounds, voice command systems, and connected cars, users can indulge in operational efficiency, saving costs & experiencing a better customer experience in local markets or retail industries.
Healthcare IoT
With our wearable health monitors, smart medication trackers, comprehensive healthcare data analytics solutions, vital signs monitoring, and remote patient monitoring services, users can experience a customized solution that will enable them to connect to devices and exchange data, reducing manual intervention, optimizing the use of resources, experiencing voice command systems, and increasing productivity & efficiency in hospitals or healthcare settings.
Why Daffodil Software
Recognized excellence, proven customer satisfaction
Categorized as an aspirant in global PEAK Matrix assessment
Recommended vendor for custom software development services
Mentioned as a company to watch in the AI space
Categorized as a leader in digital engineering services
25+
years of software engineering excellence
150+
global clientele
4.8
Avg CSAT score
95%
customer retention rate